The Transformative Benefits of the Toyota Production System
In the ever-evolving landscape of manufacturing, the Toyota Production System (TPS) stands as a beacon of efficiency and innovation. This article delves into the remarkable benefits that the Toyota Production System brings to industries worldwide, redefining the standards of operational excellence.
Origin and Evolution of TPS:
The roots of the Toyota Production System trace back to the mid-20th century, evolving as a response to post-war challenges. Born out of necessity, TPS has since undergone significant adaptations, incorporating cutting-edge methodologies and technological advancements to stay at the forefront of modern manufacturing practices.
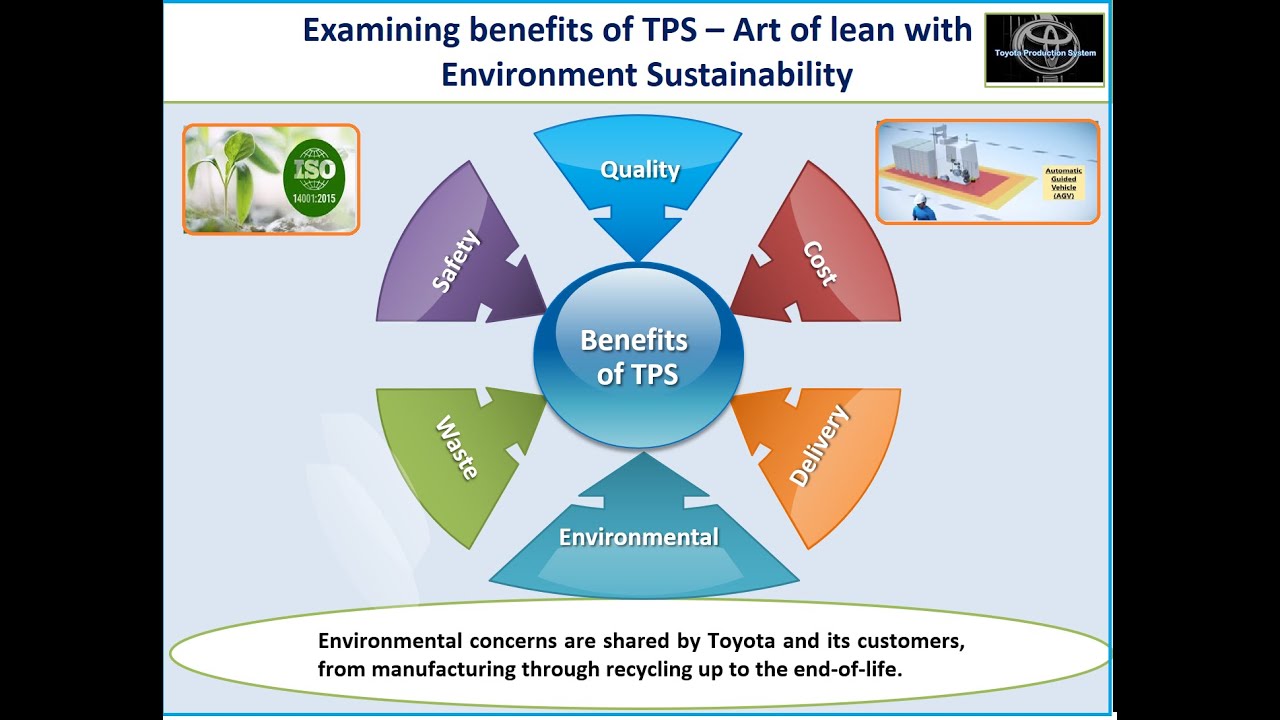
Core Principles of TPS:
At the heart of the Toyota Production System lie several core principles that form the bedrock of its success. Embracing concepts such as Just-in-Time (JIT), Jidoka (error prevention), and continuous improvement, TPS prioritizes efficiency, quality, and adaptability. These principles synergize to create a production framework that goes beyond traditional manufacturing methods.
Increased Operational Efficiency:
The primary objective of the Toyota Production System is to enhance operational efficiency. By meticulously synchronizing production processes, TPS minimizes waste, reduces lead times, and optimizes resource utilization. Real-world examples, such as Toyota’s renowned lean manufacturing success, underscore how TPS leads to streamlined operations, ultimately resulting in significant efficiency gains.
Quality Improvement through TPS:
Quality is a non-negotiable aspect of the Toyota Production System. Through the principles of Jidoka and error prevention, TPS places a strong emphasis on identifying and addressing issues at their source. This proactive approach not only ensures superior product quality but also fosters a culture of continuous improvement, where defects are seen as opportunities for refinement.
Cost Reduction Strategies with TPS:
Cost reduction is a natural byproduct of TPS methodologies. By eliminating waste, optimizing production flow, and embracing lean management practices, companies implementing TPS experience significant cost savings. From minimizing excess inventory to enhancing overall process efficiency, TPS provides a blueprint for cost-effective manufacturing without compromising quality.
Workforce Empowerment:
Beyond its impact on operations, the Toyota Production System is a catalyst for empowering the workforce. TPS encourages employee involvement in decision-making processes, fostering a sense of ownership and accountability. This section explores how TPS not only optimizes production lines but also nurtures a workplace culture where individuals are valued contributors to the organization’s success.
Flexibility and Adaptability:
In the dynamic landscape of modern business, adaptability is a key differentiator, and TPS excels in this arena. This section dives into how the Toyota Production System equips organizations to swiftly adapt to changing market demands. The principles of TPS, such as flexible production and quick adjustments, make it a robust framework for industries facing rapid shifts and uncertainties.
Case Studies and Success Stories:
Real-world applications of the Toyota Production System provide compelling evidence of its effectiveness. Through detailed case studies and success stories, this section illustrates how companies across diverse industries have successfully implemented TPS, showcasing tangible results in terms of efficiency, cost-effectiveness, and overall operational excellence.
Implementing TPS in Diverse Industries:
While TPS has its roots in the automotive industry, its principles are far-reaching. This section explores how organizations outside traditional manufacturing, including service industries, healthcare, and technology, have embraced and adapted TPS to enhance their processes. The versatility of TPS is examined through examples that demonstrate its applicability across various sectors.
Challenges and Solutions in TPS Adoption:
Implementing the Toyota Production System is not without its challenges. This section addresses common obstacles organizations may face during TPS adoption, such as resistance to change and cultural shifts. Moreover, it provides practical solutions and insights to guide businesses through a successful TPS implementation, mitigating potential roadblocks.
Future Trends in TPS:
As industries continue to evolve, so does the Toyota Production System. This section explores emerging trends and advancements within TPS. From the integration of Industry 4.0 technologies to new approaches in lean thinking, understanding the future trajectory of TPS helps organizations stay ahead of the curve in an ever-changing business landscape.
Frequently Asked Questions (FAQs)
1. Q: What distinguishes the Toyota Production System (TPS) from traditional manufacturing methods?
A: TPS is characterized by principles such as Just-in-Time production, Jidoka (error prevention), and continuous improvement, focusing on efficiency, quality, and adaptability.
2. Q: How does TPS contribute to increased operational efficiency?
A: TPS achieves operational efficiency by minimizing waste, reducing lead times, and optimizing resource utilization. Real-world examples showcase its success in streamlining operations.
3. Q: Can TPS improve product quality, and how?
A: Yes, TPS places a strong emphasis on quality through principles like Jidoka, which addresses issues at their source, fostering continuous improvement and ensuring superior product quality.
4. Q: In what ways does TPS lead to cost reduction in manufacturing?
A: TPS achieves cost reduction by eliminating waste, optimizing production flow, and embracing lean management practices. It provides a blueprint for cost-effective manufacturing without compromising quality.
5. Q: How does TPS empower the workforce within an organization?
A: TPS empowers the workforce by encouraging employee involvement in decision-making processes, fostering a culture of ownership, and accountability, and valuing individual contributions.
6. Q: Is TPS adaptable to changing market demands, and how?
A: Absolutely. TPS equips organizations with the flexibility to adapt swiftly to changing market demands through principles like flexible production and quick adjustments.
7. Q: Can TPS be implemented in industries beyond manufacturing?
A: Yes, TPS is versatile and applicable beyond traditional manufacturing. This section explores successful implementations in service industries, healthcare, and technology.
8. Q: What are the common challenges organizations face when adopting TPS?
A: Challenges may include resistance to change and cultural shifts. This section provides practical solutions and insights to guide businesses through a successful TPS implementation.
9. Q: How does TPS contribute to future trends in manufacturing?
A: TPS adapts to future trends by integrating Industry 4.0 technologies and new approaches in lean thinking. Understanding these trends helps organizations stay ahead in a dynamic business landscape.
10. Q: Are there training programs for TPS, and do they offer certifications?
A: Yes, TPS training programs are crucial for effective implementation. This section highlights the importance of training and provides information on institutions offering TPS certifications.
Conclusion:
As we navigate through the myriad benefits of the Toyota Production System, it becomes evident that TPS is not just a methodology; it’s a paradigm shift in the way organizations approach production. This conclusion summarizes the transformative impact of TPS, emphasizing its role in reshaping industries, driving efficiency, and fostering a culture of continuous improvement.